計測・分析技術室 ナノ・マイクロ領域技術班 福永 鷹信
1. はじめに
私は派遣先である機械工学部門 生体工学講座 熱物質移動研究室において、凍結手術用クライオプローブの凍結シミュレーションや、生体内熱輸送特性を可視化する新たな画像診断技術の開発などの研究業務、およびその補助に携わっています。今回は、私の業務の一つである微細加工技術を用いた業務依頼の内容についてご紹介させていただきます。
まず微細加工技術とは、主に1mm以下の形状寸法を加工するもので非常に小さく、顕微鏡等を用いなければそのものを見ることすらできない大きさのものを、加工・作製する技術のことです。加工する対象物はシリコンウエハーで、工具を用いた切削加工等ではなく、特殊なガスや溶液を用いて表面を少しずつ削っていくことにより、目的の形に成形していきます。微細加工は、加工結果に及ぼす作業の要素数が多いため、一つ一つのステップを確実に確認しながら、かつそれらを精確に積み重ねて成り立つ、非常に根気を必要とする作業です。
2. 業務内容について
主には、派遣先から依頼されるMEMSセンサの作製を行っていますが、時折技術部を通して他部門からの加工依頼を頂くこともあり対応しています。まず初めに紹介するのは派遣先依頼のMEMSセンサで、図1のような川に懸架してある橋のような構造を有するセンサです。横向きに一本かかっているのがセンサ部分で、寸法は長さ10μm、幅は1μm、厚みは40nmと非常に小さく(図2)、とても直接加工をして作製することはできないものとなっています。橋の部分は蒸着された金属からなり、ヒーターとして通電加熱することや、カーボンナノチューブやグラフェンなどを乗せて保持させることが可能となっています。
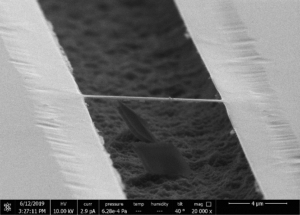
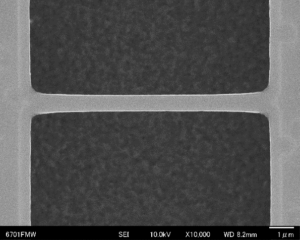
微細加工の難しさは先にも述べたのですが、次に実例をいくつか紹介させていただきます。図3は私が微細加工を始めたばかりの頃に、派遣先研究室からの依頼で作製したMEMSセンサ(図2と同じパターンのもの)です。ご覧いただくと、センサ部の左端が繋がっておらず破断していて、かつセンサの根元部分にヒビが入ってしまっています。作製工程を終えた後に、センサがこのような形になっていることを電子顕微鏡で発見すると残念な気持ちになるのですが、このような結果であってもセンサは我々に結果をきちんと教えてくれているので、それを見極めて解決するのが技術職員の役割であると考え、原因の究明を行い、工程の見直しを行います。この場合は蒸着後の金属薄膜に200度程度でアニール処理を施し、金属の残留応力を除去した上で後の工程を進めることで、以降、四隅にヒビのないセンサを安定的に作ることに成功しました。
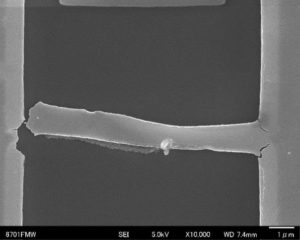

もう一つは実験をしているときに起こる問題で、静電気によるセンサ部分の溶断です(図4)。図2と同じパターンのセンサだったのですが、使用しているときに静電気がセンサ部分を流れたことにより、センサ中央部が過剰に発熱し溶けて、両端に丸く残った形状をしています。冬場によく起きる静電気はMEMSにとっては天敵で、何気ない動作がセンサを壊してしまうことに繋がります。加工後に起きる使用中の問題ですので、対処が限られており、例えば、実験環境を多湿状態で行うこと、化繊の衣類を避けて実験を行うこと、除電を的確に行うことが挙げられます。
一方の他部門の先生からの加工依頼では、三辺が50μm程度の立体物を規則正しく配列させるものや、PDMS(ジメチルポリシロキサン;合成高分子の一種)転写用のモールドとして、幅および深さ50μmのラインアンドスペースを作製しました。 図5および6はその加工例で、ラインアンドスペースと凸型形状を有するPDMSの転写用のモールドです。基本的に2次元平面(X-Y平面)に任意のパターンを書いて、その後Z軸方向に掘っていくイメージとなります。

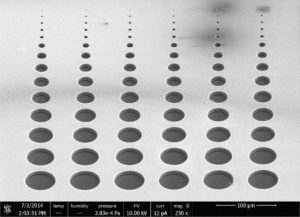
3. 加工の流れ
基本的な作製手順を図7に示します。まず、シリコンウエハーに電子線描画用のレジストをスピンコーターで塗布し(①)、依頼に応じたパターンを描画します(②電子線描画)。電子線に曝されたレジストは専用の溶液に溶けるようになるため、現像処理を行って目的となるパターン部分のみが露わになる状態にします(③現像)。次に、深掘りのための保護膜となるクロムを真空蒸着します(④クロム蒸着)。クロムはシリコン基板一面に均一に成膜されるわけですが、現像を行った後の残存したレジスト上のクロムは、剥離の工程でレジストと共に除去されるため、描画したパターンの上部にのみクロム膜が残った状態にすることができます(⑤剥離)。その後、異方性を持たせた深掘りエッチングにより、パターンを保ったまま掘り進め立体構造物を作製していきます(⑥深掘りプロセス)。最終的に残ったクロム膜および酸化膜を除去し、上面をすべてシリコンの状態にすると完成です(⑦)。
図7 微細加工の手順
4. おわりに
今回は代表的な微細加工の作製例を挙げさせていただきました。おおよそのスケール感としては、最小線幅500nm程度のパターンを描画して加工したり、50μm四方のパターンを深さ50μm程度まで深掘りしたりすることができます。また、深さ50μm程度の貫通穴やスリット加工も実績としてありますので、参考にされてください。
加工に必要な装置は、工学部技術部ではなく派遣先部門の研究室が所有していますので、加工依頼の際は内容の詳細や費用等の詳細を相談させていただきます。しかしながら、工学部技術部でも今後実績を積んでいきたいと考えていますので、教育・研究関係で微細加工をご希望の場合は是非ご連絡いただければと思います。
最後に、これらの技術は九州大学に入職して一から身につけた技術です。何の知識も持ち合わせていなかった新人時代に、懇切丁寧に技術指導をくださいました、計測・分析技術室 室長補佐 生田氏にこの場を借りて感謝申し上げますとともに、これからも変わらずのご指導をいただききますようお願いいたします。さらに、派遣先研究室の髙松教授ならびに学生さん一同には、加工プロセスの検討やトラブルシューティングにおいて、長年大変お世話になりました。派遣される時間も限られてはいますが、今度ともよろしくお願い申し上げます。