工学部技術部 製作技術室 設計・加工班 狩俣 貴大
1. はじめに
私の派遣先は機械工学部門の燃料電池システム研究室というところで、そこでは研究内容に沿った実験装置の仕様・設計の相談から、製作・組み立てまでを行っています。技術部では、主に半自動NCフライス旋盤や放電加工機を担当しています。
ここでは、昨年度に依頼を受けた業務の中で特に難易度の高かった「鉛」の加工について、失敗例を交えながら紹介いたします。依頼内容としては、60×60×t30mmの鉛にφ1.5mmの貫通穴もしくは1.5mm辺の四角穴を、肉厚0.5mm間隔で676個開けるというものでした。
2. ドリルによる加工
まず初めにドリルで加工してみました。最初の1穴は加工できましたが、その隣に穴を開けようとすると、肉厚の薄い隣の穴に吸い寄せられるように穴が曲がり、貫通してしまいました。
このような穴壁の一方の厚さが薄い加工の場合、加工する穴が曲がる現象はよく起こります。そのため、様々な注意点に気を配り加工するのですが、今回の依頼は、小径かつ穴深さが工具径の20倍もあるような深穴加工であるため、細く刃長の長い(工具剛性が低い)ドリルを使わなければならないことと、材料が鉛という硬度の低い(比較的軟らかい)金属であることが、より困難な加工にしていました。そこでドリルによる切削加工を諦め、放電加工機を用いることにしました。
3. 放電加工機による加工
ワイヤ放電加工機(図1)と形彫り放電加工機(図2)の2台を使用して加工を試みました。上記どちらも、水や油等の液体中で工具(電極)と材料の間の数ミクロンの隙間に、1秒間に1000~10万回の火花を断続的に飛ばし、熱により金属を溶かしながら加工する機械です。
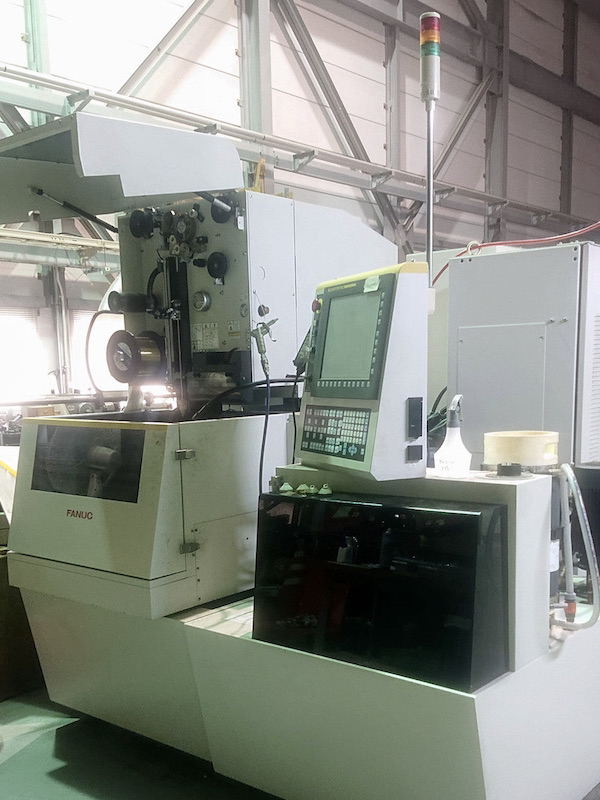
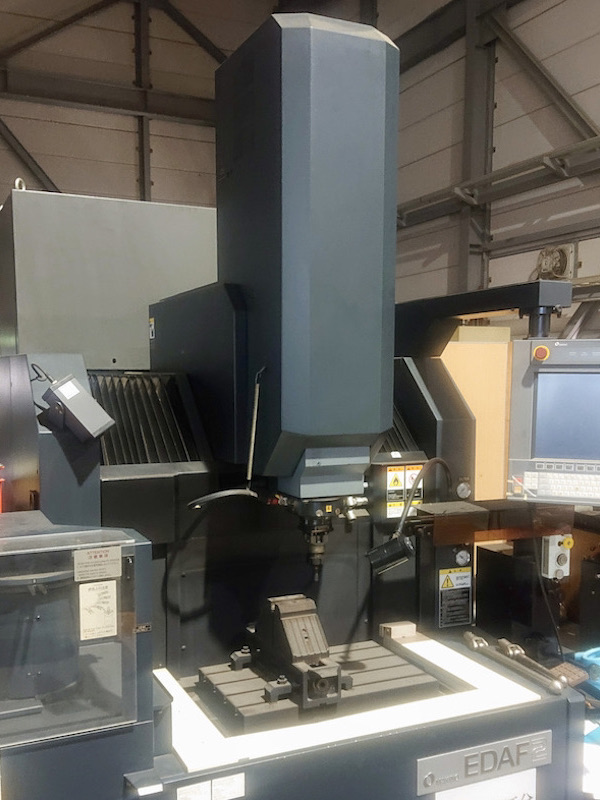
まずワイヤ放電加工機で専用の電極を製作し(図3)、その電極を用いて形彫り放電加工機で穴あけ加工を行いました。このとき、材料に合わせて最適な火花の電圧・電流・持続時間等の加工条件を選定する必要があります。最初の加工では、図4のように1.5mm角ではなく1.8mm角程度に穴が大きくなってしまいました。また一部壁の損壊も見られました。この後、何度も試行錯誤を繰り返して最適な加工条件を追求すること約二週間、ようやく納得がいくものを作り上げることができました。
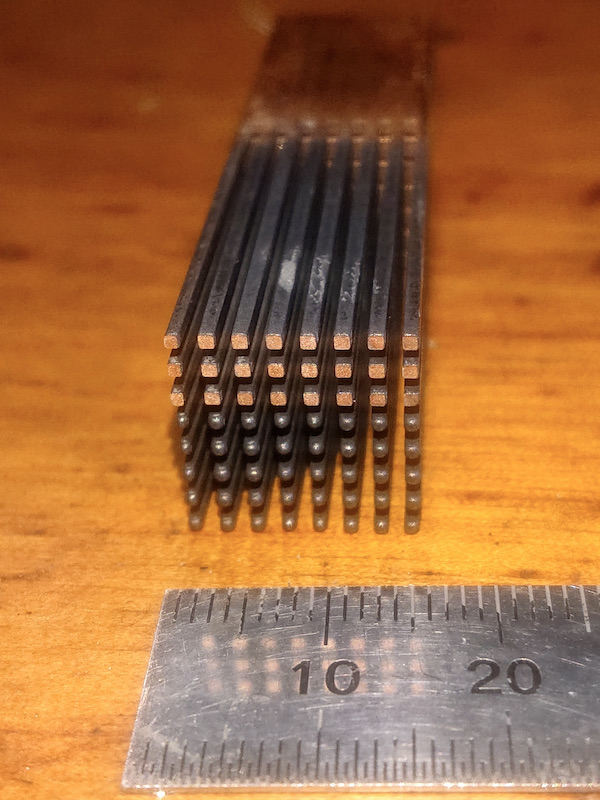
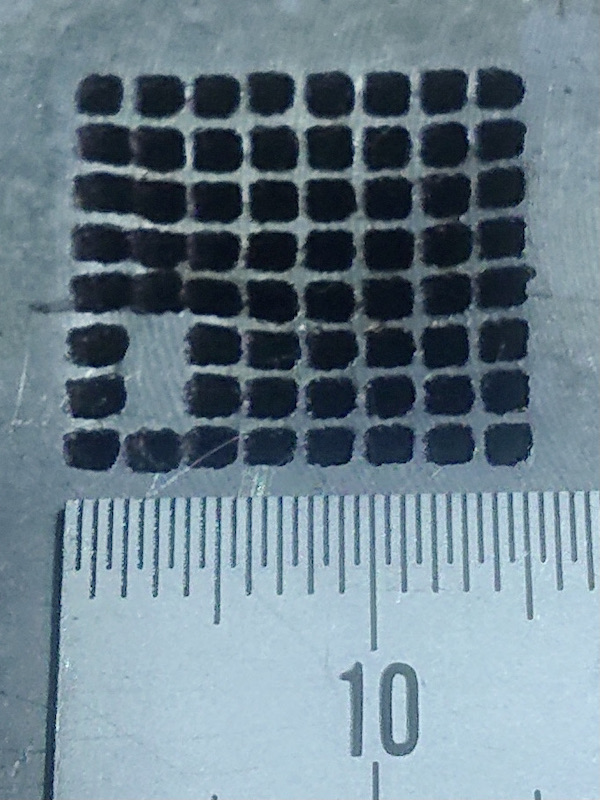
4. 完成品と改善の余地(今後の目標)
最終的には最適な加工条件を選定して加工でき、図5のような製品を完成することができました。しかし肉眼ではすべての穴の断面が正方形に見えても、電子顕微鏡で観察すると、一部の領域で正方形が2個ずれて重なっているような形状の穴になっている部分が生じてしまいました(図6)。形彫り放電加工機では加工に伴い電極が劣化していくため、必要に応じて電極を交換しなければなりません。その際電極の位置決めが上手く行かなければ、このようにいびつな穴となってしまいます。今回、電子顕微鏡による穴断面積の測定結果は、1.5×1.5=2.25mm2の仕様を満たしていましたが、次回は電極の断面積を小さくし、仕上げ代をより多く残す等の工夫を行ってより正確な加工を行いたいと考えています。
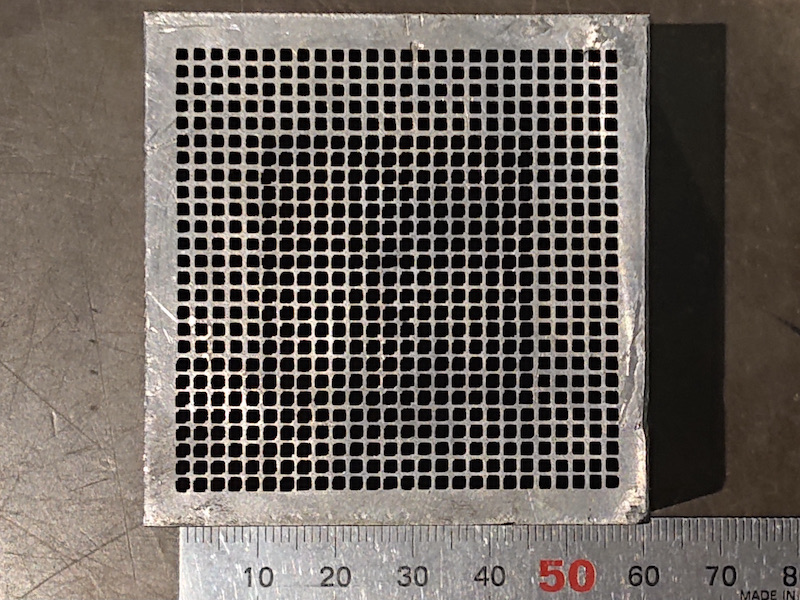
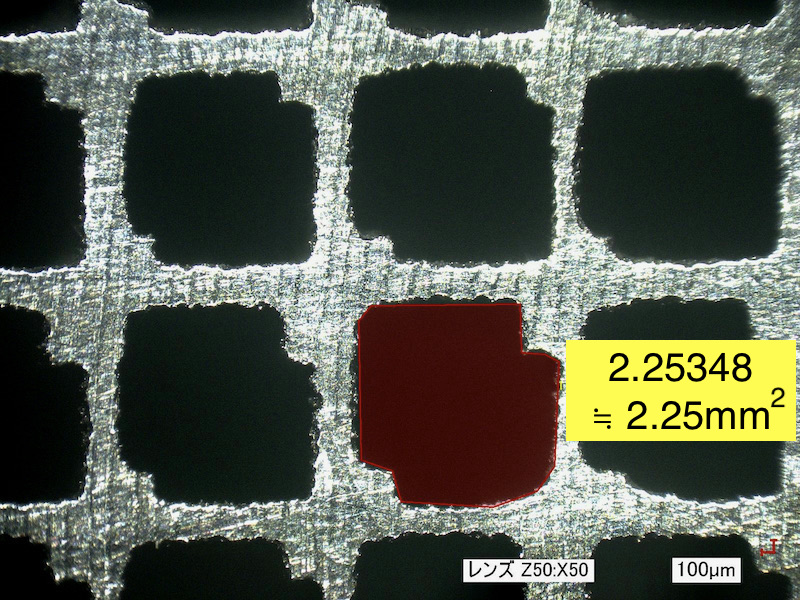
5. おわりに
今回は通常行っている金属(ステンレス・銅・アルミ等)ではなく、鉛の加工を紹介させていただきました。複雑な形状や加工が難しい材料等、製作に伴うお悩みに対して技術職員が解決のお手伝いをさせていただきます。製作技術室一同、皆様からのご依頼をお待ちしております。
最後になりましたが、今回鉛の加工に挑戦する機会をいただきました医学研究院保健学部門 藤淵 俊王先生、並びにアイソトープ総合安全管理センター 中島 裕美子先生にこの場を借りて感謝を申し上げます。